По итогам конкурса «Лучшее изобретение (полезная модель)» за 2021 год изобретение коллектива сотрудников НТЦ во главе с главным конструктором «КАМАЗа» – директором НТЦ Евгением Макаровым заняло второе место. В суть изобретения вникали корреспонденты «ВК».
Главный специалист по рамам проекта РАиСПСАК Ильгиз Мавлеев, который согласился нам помочь, работал в команде изобретателей. Он сообщил, что работа над решением проблемы, которая началась еще в 2015 году, вылилась в изобретение, и на него был получен патент.
"Традиционно изготовление лонжеронов в рамах производилось методом штамповки. При этом на одном штампе можно получить только один вид лонжерона. Но с расширением модельного ряда автомобилей менялись и рамы. Если менять длину лонжерона, то требуется изготовление нового штампа, а штампы – достаточно дорогие элементы, с долгим сроком окупаемости. А для мелкосерийных образцов и вовсе не окупаются", – пояснил Ильгиз Рифович.
Поэтому перед конструкторами НТЦ была поставлена задача: новые семейства автомобилей К4 и К5 разработать на базе лонжеронов с постоянным профилем так называемого швеллерного типа. Преимущество такого лонжерона в том, что он формируется из одного длинного рулона листового металла в П-образный профиль, и его можно обрезать на нужную длину.
"Возглавил группу главный конструктор «КАМАЗа» – директор НТЦ Евгений Макаров. В нее вошли все конструкторы конструкторского бюро рам, в том числе я, начальник конструкторского отдела агрегатов шасси (КОАШ) Владимир Орлянский, главный специалист рам и сцепных устройств КОАШ Константин Холопов, главный специалист рам и сцепных устройств – руководитель группы КОАШ Рустем Шамаров, главный специалист по сопровождению серийного производства Сергей Султанов", – перечислил Ильгиз Мавлеев.
По его словам, потребовалось кардинально пересмотреть переднюю часть рамы, где появились большие кронштейны, отлитые из высокопрочного чугуна. На кронштейны крепились навесные агрегаты и узлы – кабина, подвеска, рулевой механизм и т.д.
Получившиеся лонжероны с постоянным профилем типа рамы сначала опробовали на ряде автомобилей поколения К3. И уже впоследствии, решив возникшие проблемы, приступили к проектированию рам автомобилей семейства К4.
"Разработка рам семейства К4 заняла около года, достаточно долгий срок. Но это было связано не с самой рамой, а с производством автомобиля в целом, ведь это был уже не серийный, привычный нам КАМАЗ, а современный грузовик, практически все узлы которого были оригинальными", – пояснил конструктор Мавлеев.
Он добавил, что с применением лонжеронов постоянного сечения также была введена сетка отверстий на боковой поверхности с шагом 50 мм, так называемый перфорированный лонжерон. Это позволяло двигать навесные узлы с шагом 50 мм. Для сравнения: на штампованных лонжеронах, чтобы подвинуть какой-либо агрегат, нужно было изготовить новые отверстия под новое положение.
"Впоследствии, устранив некоторые проблемы, выявленные в процессе эксплуатации автомобилей семейства К4, такой тип рам с лонжеронами постоянного сечения был перенесен и на новое поколение КАМАЗов семейства К5", – резюмировал Ильгиз Рифович.
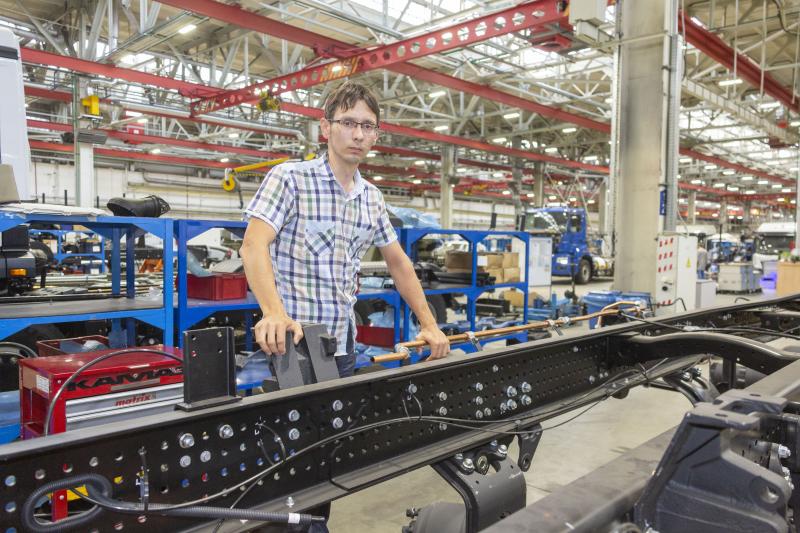
Ильгиз Мавлеев демонстрирует лонжероны постоянного сечения, которые успешно используются в КАМАЗах поколения К5
Текст: Татьяна Парамонова. Фото: Виталий Зудин