Создание такого титана как литейный завод «КАМАЗа» не могло быть лёгким. А установленные сроки и значимость, придаваемая проекту государством, и вовсе приравнивала его к подвигу. «КАМАЗ», а вместе с ним и литейный завод, рассматривался как некое предприятие будущего – с высокой производительностью, стабильной эффективностью и высокой культурой труда. Все эти показатели следовало предусмотреть на самых ранних этапах проектирования и строительства.
Подготовкой технического задания занималось сразу несколько организаций. Корпус ковкого и серого чугуна (сейчас производство чугунного литья) разрабатывал литейный отдел СПТУ ЗИЛ, на корпус цветного литья работал Ярославский институт «Гипродизель», стальным корпусом занимался головной институт автомобильной промышленности «Гипроавтопром». Первые камазовские литейщики также активно участвовали в этой работе как заказчики. Все понимали: им выпал шанс создать новый, современный завод.
Перед СПТУ ЗИЛ была поставлена сверхзадача – спроектировать корпус «на голову выше» ведущих мировых чугунолитейных производств. Сенсацией того времени был завод компании «Форд» во Флэт-Роке, США, оснащённый электрическими дуговыми печами, в противовес вагранкам и индукционным установкам, которые были в ходу у основной массы предприятий в мире. Для советских литейщиков электродуговые печи тоже не были в новинку, но плавили в них, в основном, сталь, а не чугун. И по этому вопросу было сломано немало копий на совещаниях. Единство мнений было достигнуто лишь к 1972 году: оснастить КСКЧ десятью индукционными печами плавки и девятью индукционными канальными печами выдержки ёмкостью по 60 тонн. Но на заключительном совещании у министра автомобильной промышленности СССР А.М. Тарасова было принято решение укомплектовать завод электродуговыми печами плавки, как на заводах Форда в США.
Но вернёмся в конец 1971-го. Технические задания на все корпуса будущего литейного завода, наконец, готовы. Впервые в отечественной истории строительства литейных производств были заложены двухэтажные литейные корпуса. Все вспомогательные, пылевыделяющие, операции были размещены на первом этаже. Литьё после охлаждения выбивалось туда и транспортировалось подвесными толкающими конвейерами на второй этаж. Формовочная смесь после выбивки также проваливалась на первый этаж и проходила подготовку к возврату на повторное использование. Большинство систем отопления и промышленная вентиляция тоже были вынесены вниз. Такая технологическая цепочка позволяла улучшить экологию второго этажа, где было сконцентрировано основное производство. Техпроцессы становились прямолинейными от заливки до сдачи. Всё это было впервые.
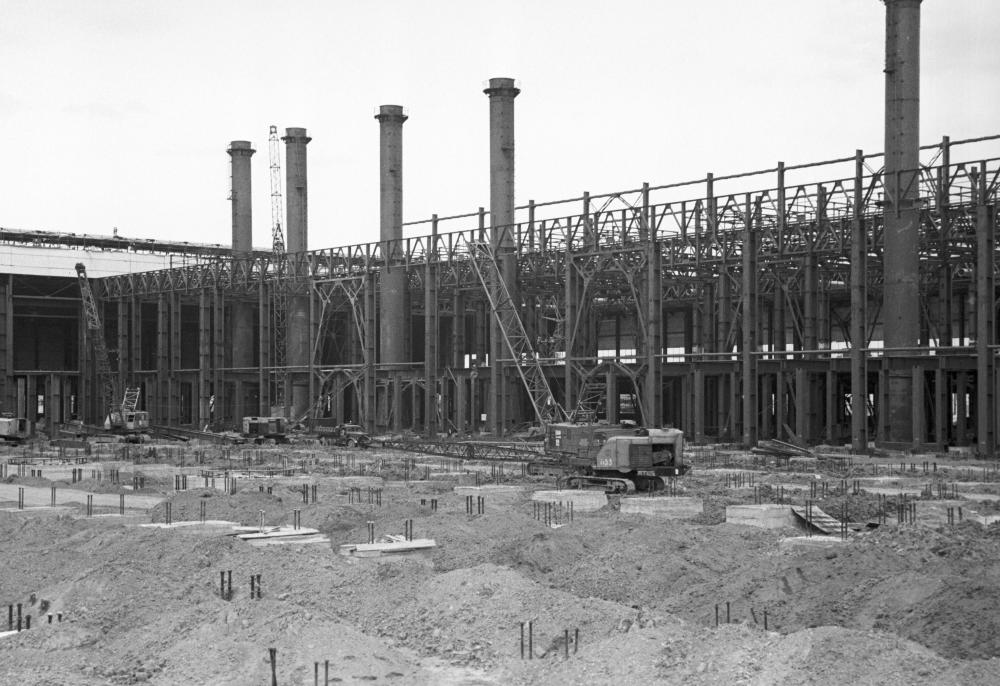
Текст: Эльвира НАСИБУЛЛИНА.
Мощнее чем у Форда!! Есть чем похвастать. А вот у Форда умудрились бы сжечь целый завод и потом десятилетиями пожимать плечами: черт его знает, как так получилось и кто виноват - не поймем...
Ответить (0)Пока живы свидетели этого-возьмите у них интервью.Я работаю на литейке 38 лет-восхищаюсь ,как они с этим справились !
Ответить (0)